So you bought a brand new furnace! Nice! All the bells and whistles! But how do you know you hired the right company, and what are the signs of a bad furnace installation?
To protect our amazing customers, your friends at Five Star Home Services will run through what bad HVAC installation looks like and how to avoid it.
Focusing on Improper Furnace Installation
Installing a new furnace is a decision that lasts you 15 to 20 years or more.
However, if you make the wrong decision with your choice of HVAC installer — the result could be a system that gives you more problems than it’s worth. In other words, a poor installation could cost you more than you bargained for!
While this is relatively rare, an installation that does everything right the first time is also rare when you hire a handyman or anyone other than Five Star Home Services. Most HVAC contractors can get your unit up and running. Unfortunately, however, this does not constitute a “good” installation.
Furthermore, this is what gives HVAC contractors a bad name. Poor work can cost you money without you even knowing about it. HVAC is a complicated industry; it’s never your responsibility to know all the ins and outs of the installation process. Because of this, a dishonest or unscrupulous company can take advantage of you and cut corners. This can be very costly. Nevertheless, your friends at Five Star Home Services are always here to help!
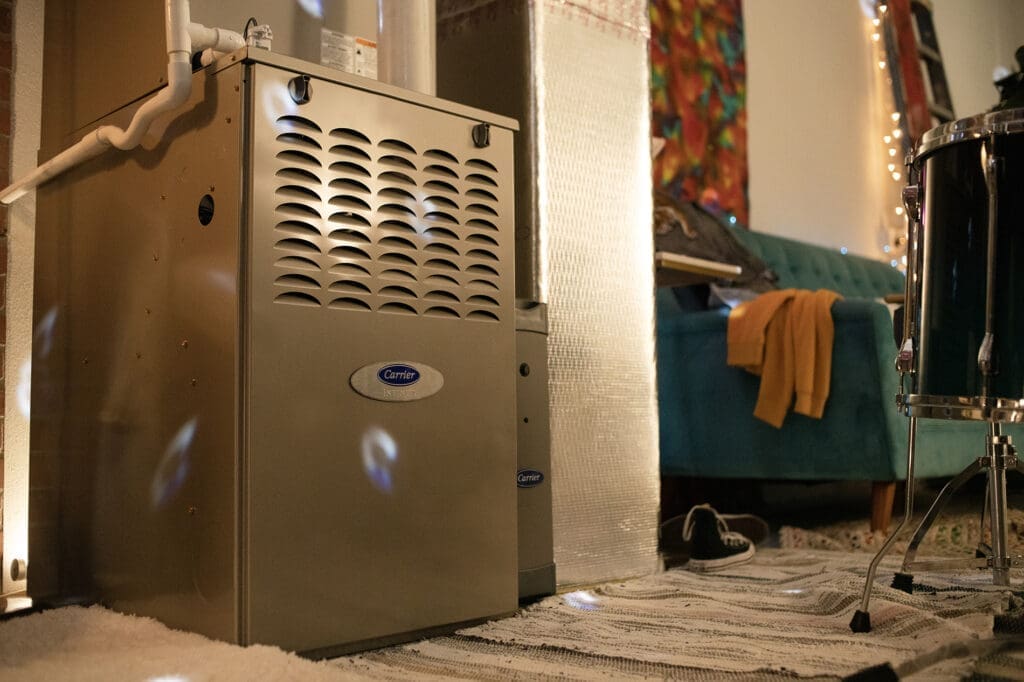
Consequences of a Bad Furnace Installation
The consequences of a poor installation job are many. They include the following:
- That last one means higher utility bills
- Shortened lifespan for your furnace
- Decreased efficiency, even if it’s a high-efficiency furnace
- Reduced comfort and more headaches as you deal with the sub-par system
Next, we will break down each of these below and what they mean. We will also discuss why they happen, and how they can be avoided. Nevertheless, the bottom line is that you’re putting several years’ worth of comfortable operation at risk when you have a mediocre installation performed.
The two primary reasons we see that lead to these problems include:
- Cutting of corners to save costs
- Lack of installer knowledge
The biggest reason why these things are so diabolical is that most sub-par HVAC installations don’t end up causing major issues for 8 to 10 years. This is why it’s tough to catch problems. HVAC contractors can just shrug their shoulders and say, “these things happen.” For the homeowner, nevertheless, this could mean having to purchase a new system 10 years later instead of 20.
While random problems do occur in HVAC systems, they happen a lot more predictably when certain steps aren’t taken.
Cutting Corners in Furnace Installations
The biggest problems we usually run into when it comes to furnace installation aren’t with the furnace itself. Believe it or not, it’s with the ductwork. Remember, HVAC systems are systems. Furnaces don’t operate alone. They require proper ventilation, ductwork, and infrastructure in order to do their job correctly. As we’ll talk about shortly, there are a few things with the furnace itself to watch for, but it’s generally everything else that gets ignored.
Return airdrops are a portion of ductwork that enable the air to travel back from your home down to the furnace. This is what enables proper airflow. The danger is when the return air drop isn’t big enough to support your furnace. This is a big problem. When this happens, your furnace is starved for air. Airflow is a must! If it doesn’t receive enough air to do its job and supply new, warmer air to the house, it’s going to cost you. Keep in mind that this is a minor charge to repair during HVAC installation. Nevertheless, it is a major difference in the performance of your furnace unit.
This also brings up another area that is often neglected, which is ventilation. If you have a “standard” 80% efficiency furnace, it will generally vent out of a masonry or metal chimney flue. If it’s a 905 or higher “high-efficiency” furnace, it will require a plastic PVC drain line to vent properly.
These can be installed by anyone who installs the furnace. Nevertheless, they are not always installed well. For one, the PVC pipe can only be so long before it’s no longer within manufacturer specifications. From there, you start to run into problems. Additionally, if the piping has to go through multiple turns before it reaches outside, this adds to the length. Additionally, too many turns can result in your furnace breaking down due to vented air backing up into your system.
Likewise, the PVC pipe needs to be shifted to a certain angle. I have seen many that are level instead of angled. When this is the case, it means your HVAC unit won’t vent and drain properly. This can cause long-term problems.
Although there other corners that can be cut during installation — listing them all would take too long.
In short, we will cover some other areas below, but these are the most frequent ones we’ve seen as we talk to homeowners about their home heating needs.
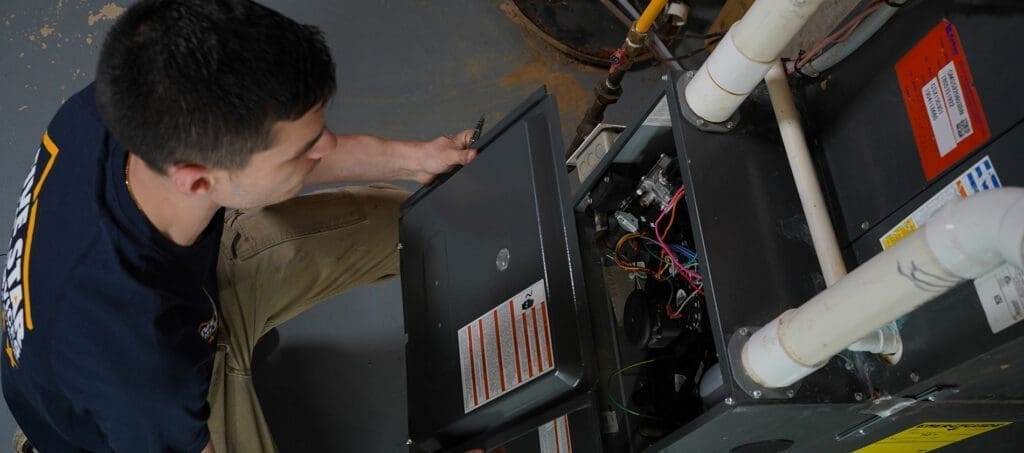
Calibrating, Commissioning, and Matching
Calibration, commissioning, and matching of furnace equipment are essential for ensuring the effectiveness and longevity of the equipment. Calibration ensures that the equipment is running at its optimal efficiency and producing accurate results. Commissioning is a comprehensive process that validates if the equipment has been installed correctly and is operating as per its intended design. This process includes quality assurance testing and fine-tuning of the equipment to ensure its efficiency and reliability. Moreover, the process of matching involves ensuring that different components of the equipment work harmoniously with each other, thus reducing the chances of equipment failure. In summary, these processes are essential to ensure the reliability, safety, and efficiency of furnace equipment.
Additionally, calibration, commissioning, and matching are not one-time processes. They need to be regularly performed to maintain the efficiency and effectiveness of furnace equipment. Regular calibration ensures that any changes in the equipment’s performance are identified and corrected promptly, reducing downtime and minimizing costs. Commissioning should also be repeated after any major repairs or modifications to the equipment to ensure its proper functioning.
Similarly, matching should be continuously monitored and adjusted as needed to maintain the equipment’s optimal performance. Additionally, regular maintenance and inspection of furnace equipment is essential for identifying potential issues before they become major problems.
Aside from ensuring proper functioning, calibration, commissioning, and matching also play a significant role in safety. Accurate readings and precise control of temperatures are crucial in preventing accidents or equipment malfunctions that could result in harm to workers or damage to the surrounding environment.
Moreover, proper calibration, commissioning, and matching also help to prolong the lifespan of furnace equipment. Regular maintenance from Five Star Home Services, along with fine-tuning, ensures that the equipment is not overworked or operating at suboptimal levels, thus reducing wear and tear.
Under Pressure: The Missing Metrics of Furnace Testing
We don’t think we can stress enough. Far too often pressure testing is skipped. This can mean trouble for the life of your home heating system!
Take gas pressure, for instance. A lot of furnaces use some form of gas as fuel. If a gas valve has a traditional valve that requires a wrench to close, we’ll remove it and install one that a homeowner can operate by hand. This is excellent for emergencies, and it is a necessary safety precaution.
However, when a furnace changes, the necessary gas pressure to fuel it might also change. If your HVAC installer isn’t testing this (as many of them don’t), they’re leaving it to chance. This isn’t good!
Additionally, static pressure is another major culprit. Static pressure deals with the pressures of the air on your HVAC system during almost every stage of the heating and air conditioning process. Static pressure can kill a system years before it needs to be replaced; it includes the ductwork size and shape, the air filter, the blower motor, and the furnace itself. As such, it requires a lot of testing to make sure everything is operating smoothly like it should. Even something simple like moving a furnace from an open area to a smaller room or basement closet can hinder airflow. If you want to get the most out of your home heating system, you need to account for this.
In any case, far too few HVAC companies check static pressure after an installation. At Five Star Home Services, our technicians make sure to check static pressure on all their work!
Dangers of a Poor HVAC Installation
The biggest dangers aren’t the things we talked about earlier such as costs and shortened lifespans. These things are bad too. Don’t get us wrong. However, it isn’t the main reason this continues to happen. The biggest danger is that homeowners don’t know these things. Because of this, companies can skip some or all of these. They are then never held accountable. We feel this is unacceptable and we know a lot of homeowners who would agree!
In short, this is why a big part of what we do is educational. When we go into a home, our job isn’t just to sell you something. Sure, that helps keep us in business. But what’s more important is integrity. It is our job to help you understand the considerations that go into a good HVAC decision.
Being Proactive: Do Your Homework, Make the Right Contractor Decision
Five Star Home Services is in business because we cross all of our “t’s” and dot all of our “i’s” in the furnace installation process. We can sit down at the dinner table with a potential customer and talk about all the different things we do that our competitors don’t do or try skipping over. It’s what enables us to look you right in the eye!
Because so many contractors are cutting corners to remain competitive and cheap (instead of educating homeowners), we have to remind customers that cheaper isn’t always better. Even though a mediocre installation for less money might seem like a better deal, you will pay for it one way or another.
Five Star isn’t always going to be the right choice for customers. We understand this. There are other companies doing good work, both here in the Columbus area and throughout Greater Dayton and Greater Cincinnati.
However, we wouldn’t be writing this article if it weren’t a big problem. In short, this is why HVAC as a whole sometimes gets a bad name. But we are here to reconcile that! We encourage you not to let yourself be taken advantage of in the home comfort contractor search. Aggressively educate yourself and be prepared! We are always here to help!
Call us anytime at (833) 405-8009!